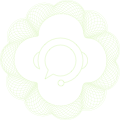
Cost of goods sold (COGS) is the direct cost of producing goods, excluding overhead costs. This metric is important, as it represents the amount of product you have to sell to break even or make a profit. Conversely, the total manufacturing cost Bookkeeping for Chiropractors formula does include overhead costs.
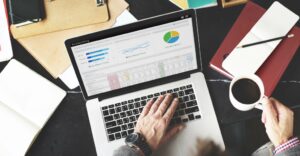
What is Manufacturing Overhead?
This includes direct costs such as raw materials and labor, as well as indirect costs like overhead expenses. Knowing how to calculate total manufacturing costs is incredibly important supply chain data. If you know your inventory value, you can calculate your company’s sales margins and use that information to identify where you could trim unnecessary expenses. Your total manufacturing costs are essentially an expense analysis that calculates how each of your company’s departments contributed to producing a finalized product. This looks at all stages of the manufacturing process from raw materials to work-in-progress to final result.
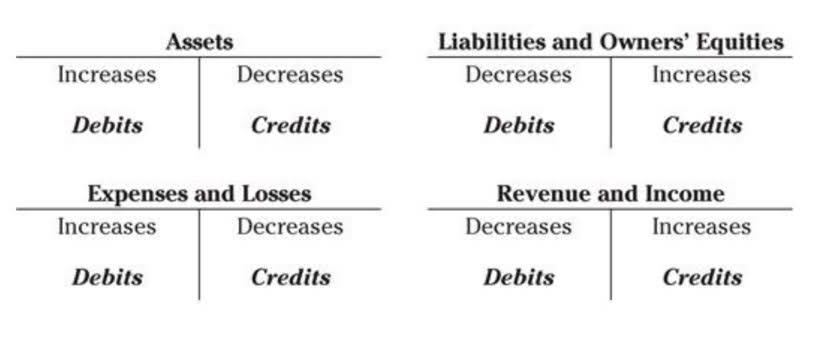
How ProjectManager Helps With Manufacturing Costs
Instead of sinking time into managing spreadsheets, inFlow consolidates information in one place and provides updates in real-time. It has the ability to create a bill of material (BOM), as well as help calculate your cost of goods sold. Gone is the need to monitor stock levels and contra asset account calculate potential output– inFlow does it all instead.
Determining Direct Materials Used
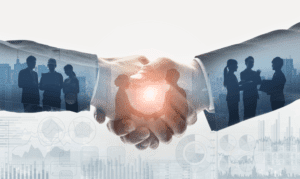
The value of these raw materials increases over the production of the product. Raw materials go through any number of types of operations in the course of manufacturing, such as welding, cutting, etc. When figuring out direct material costs, it’s important to distinguish between direct and indirect. Indirect costs are subsidiary material costs, such as shop supply costs, total manufacturing cost formula perishable tools and equipment costs. The Total Manufacturing Cost Formula is an essential tool for businesses to evaluate their production expenses comprehensively that helps financial health of company.
- With all this valuable information under your belt, you can better track manufacturing costs as they pertain to your workforce.
- When monitored closely, it can help identify inefficiencies and improve business outcomes.
- This gives a better insight into cost and profit in real-time, helping to set more informed pricing.
- Producers must take a nuanced approach when evaluating inventory to make accurate calculations.
- Manufacturing costs are only the expenses related to creating a product, while production costs are all the expenses incurred to keep an entire business operating.
- Brahmin Solutions helps by centralizing all indirect costs such as utilities, rent, and maintenance costs.
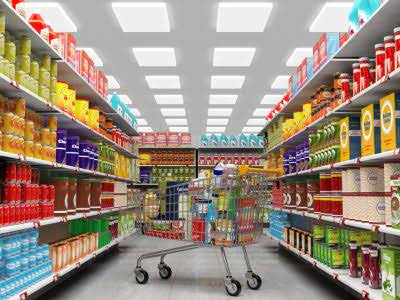
It is good practice to regularly evaluate your supply chain and to identify opportunities for improvement. Take advantage of any bulk-buy discounts or seasonal supply-side surplus to guard against off-season price increases. When looking to substitute materials for a lower-cost alternative, always ensure you are not compromising the quality of your product and potentially damaging your brand. Discrete manufacturing involves the production of distinct items, such as cars, electronics, or furniture. In this environment, overhead can fluctuate based on batch sizes, complexity, and production volumes. Manufacturing cost is essential to any business, from the smallest startup to the largest multinational corporation.
- The company has been able to do so by consistently working on improving the efficiency of production and lowering manufacturing costs.
- That’s on top of our features such as our automated workflows and task approval settings to streamline processes and ensure quality.
- Manufacturing Overhead is the manufacturing process cost that is not directly tied to producing a particular product.
- CFI is the global institution behind the financial modeling and valuation analyst FMVA® Designation.
- With the help of manufacturing costs, the company can assess the factors which are affecting the cost of the product and the areas where it can reduce the cost.
- Manufacturing companies often have difficulty finding workers with the right technical skills to fill open positions at all levels of their organizations.